Industrial Automation Solutions
Custom PLC, SCADA & Robotics
Custom Automation Solutions
At KDR Automation Ltd, we provide tailored industrial automation solutions to enhance productivity, efficiency, and reliability in manufacturing environments. Our expertise spans PLC programming, robotics, SCADA systems, and Industry 4.0 technologies, ensuring that your factory operates at peak performance.
Process Analysis & Design
Our team conducts detailed process assessments to identify inefficiencies and automation opportunities. We leverage our experience in industrial automation to design scalable and future-proof systems that deliver measurable ROI, optimising everything from production line control to energy efficiency.
System Implementation & Integration
We specialise in the seamless integration of automation technologies into your existing infrastructure, minimising downtime and ensuring a smooth transition. Whether implementing PLC and SCADA systems, integrating robotics, or deploying IoT-connected solutions, our engineers ensure that every project aligns with industry best practices and compliance standards of automation technologies with your existing infrastructure, minimising downtime.
System Digital Twin & Virtual Commissioning
To reduce risk and accelerate deployment, we utilise Digital Twin and Virtual Commissioning methodologies, allowing for extensive pre-deployment testing. This approach reduces commissioning time, lowers costs, and ensures optimal system performance before physical installation.
Ongoing Support & Optimisation
Automation doesn't end at implementation. We offer remote monitoring, predictive maintenance strategies, and system upgrades to keep your automation systems running at their best. Our team provides long-term support, ensuring your operations continue to benefit from the latest advancements in automation technology.
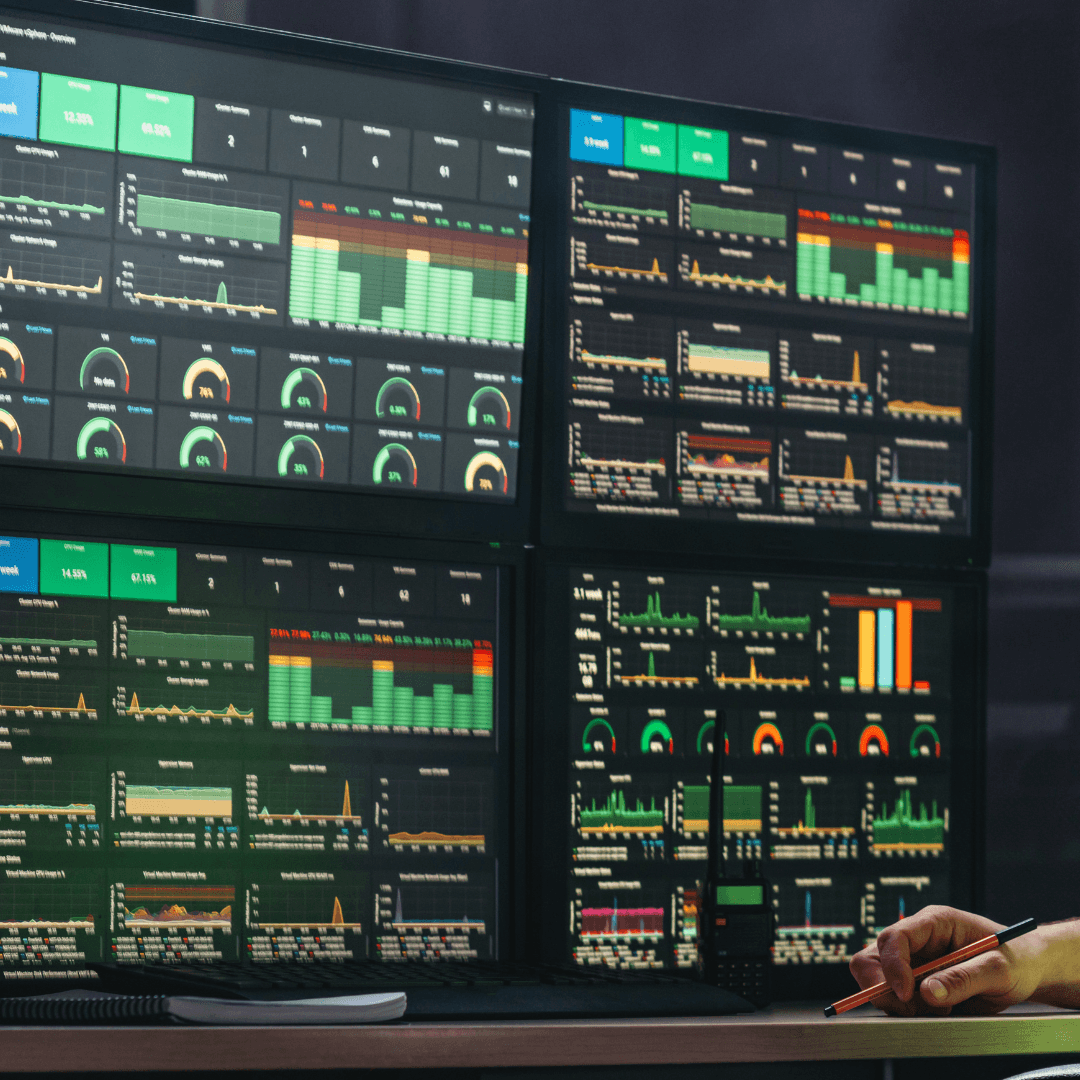
Brands
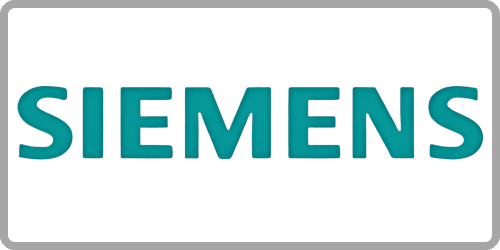
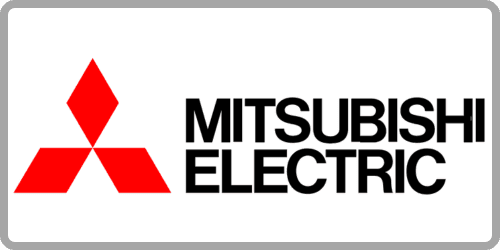
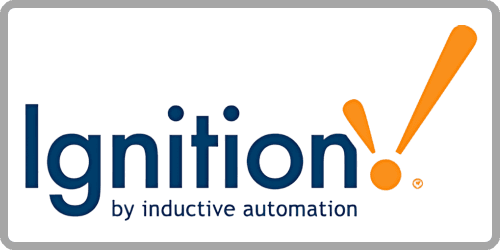
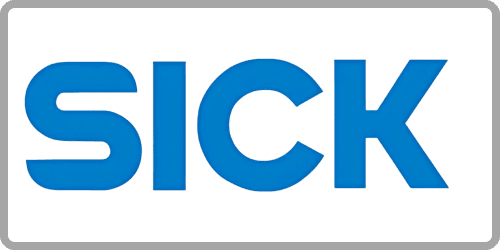
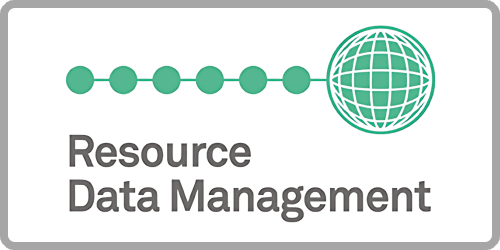
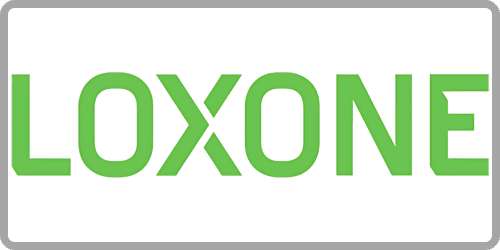
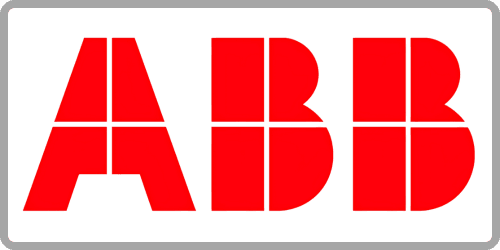
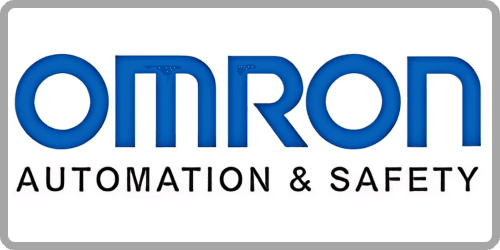
Industries
Ready to transform your manufacturing process?
Get a Free ConsultationFrequently Asked Questions
Frequently Asked Questions
How long does an automation project typically take?
Implementation timelines vary based on complexity, but most projects deliver measurable productivity gains (typically 30-40% efficiency improvements) within 3-9 months from design to commissioning.
Can you automate legacy equipment?
Yes, we specialise in retrofitting older machinery with modern automation controls to extend equipment life while achieving enhanced product consistency through precise, repeatable processes.
Will automation replace human workers?
No, automation enhances worker safety by handling hazardous tasks while allowing your team to focus on higher-value activities. Our solutions are designed for human-machine collaboration.
What are the typical cost savings of automation?
Businesses achieve 20-40% operational cost reductions through lower energy consumption, material waste reduction, and optimised workflows – with 24/7 monitoring providing additional efficiency insights.
Do you offer ongoing support and maintenance?
Yes, our support includes predictive maintenance and real-time monitoring to maintain your 40%+ productivity gains long-term, plus system upgrades as your needs evolve.
Can automation help with regulatory compliance?
Absolutely. Automated quality control reduces defects by up to 90% while ensuring full traceability – critical for meeting strict industry standards and audit requirements.
How does automation improve production quality?
Our systems deliver enhanced product consistency through precision repeatability, typically reducing variability by 60-80% compared to manual processes.
What safety benefits does automation provide?
Automation minimises worker risk by handling dangerous tasks in high-temperature, heavy-lifting, or hazardous material environments – while maintaining 100% safety compliance.