Machine Safety Systems
Compliant Safety Solutions
Machine Safety Systems
Compliance with UK and EU safety standards for all industrial equipment, ensuring worker protection and regulatory conformity.
Your Safety, Our Priority
We ensure your equipment meets all safety requirements so you can:
- Operate with confidence - Our certification guarantees compliance with international safety standards
- Reduce workplace risks - We identify potential hazards before they become problems
- Protect your team - Verified safety measures that meet strict occupational requirements
- Avoid costly downtime - Proper safety systems mean fewer unexpected shutdowns
- Meet legal obligations - Full compliance with regional equipment directives
Safety Components That Protect Your People
We implement reliable safety solutions including:
- Smart detection systems - Instant response when workers enter danger zones
- Emergency controls - Quick shutdown options when seconds matter
- Operator safeguards - Designed to prevent accidents before they happen
- Access protection - Keeps unauthorized personnel away from hazards
- Future-proof technology - Systems that adapt as your needs change
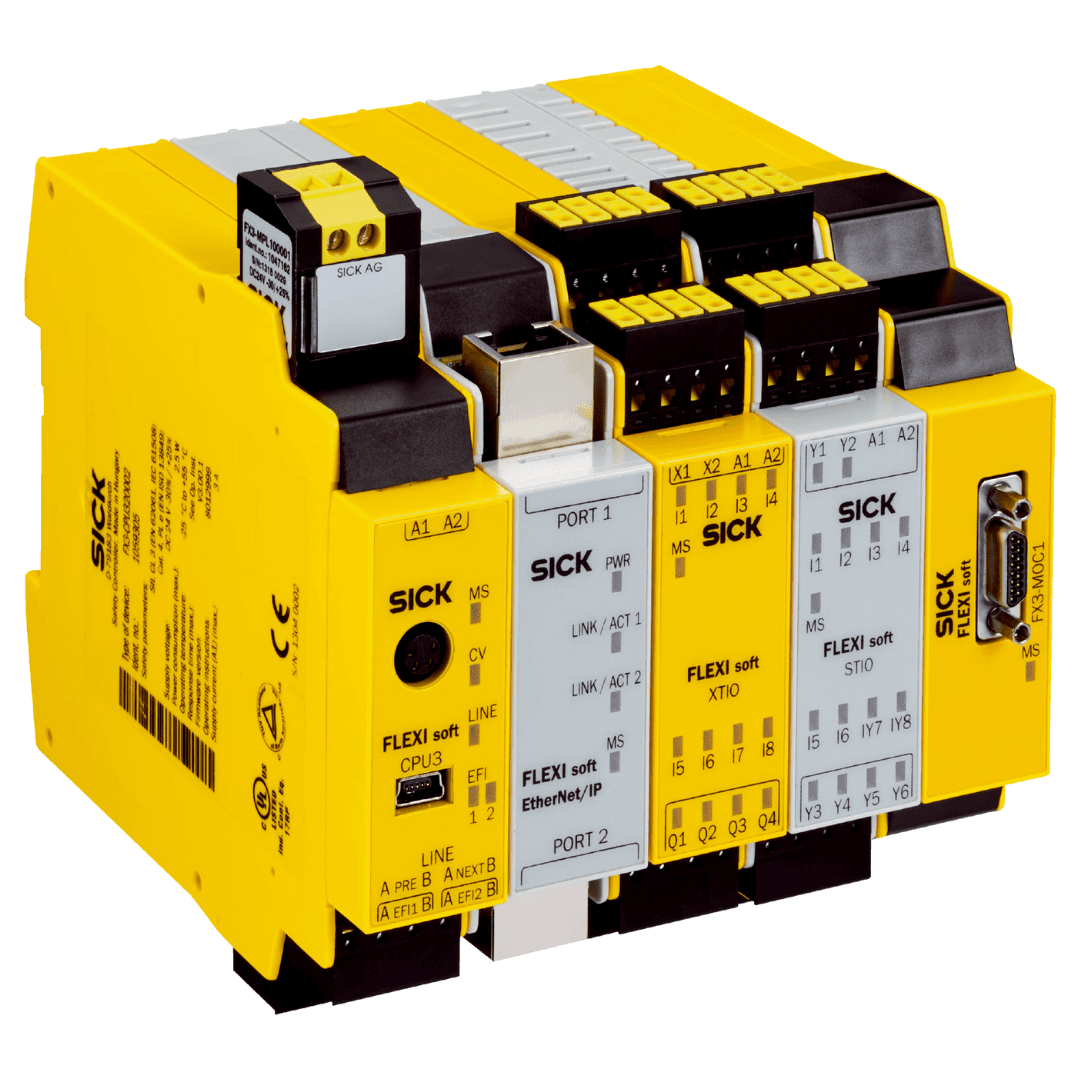
Our Safety Services
Risk Assessments
Risk assessment, hazard analysis and risk reduction
Safety Upgrades
Retrofitting legacy equipment to current standards
Guard Design
EN ISO 14120 compliant machinery guarding
Validation
Safety function verification and documentation
Need compliant safety solutions for your equipment?
Request Safety AuditFrequently Asked Questions
Frequently Asked Questions
What safety standards apply to robotic workcells in industrial settings?
We ensure compliance with UK and EU regulations, including ISO 10218 (robots and robotic systems) and ISO/TS 15066 (collaborative robots). Our solutions cover risk assessments, safety-rated stops, and proper safeguarding for both collaborative and traditional industrial robots.
How do you ensure safe human-robot collaboration in workcells?
We implement measures such as speed and separation monitoring, protective distance control, and force-limiting technologies in line with ISO/TS 15066. Our team establishes safe interaction protocols through thorough risk assessments and safety-rated stop functions.
What solutions do you offer for conveyor and production line safety?
Our production line safety systems include interlocked guards, zone control systems, and comprehensive hazard detection. We implement machine state monitoring and emergency stop circuits, ensuring compliance with the Machinery Directive (2006/42/EC) and PUWER regulations.
How do you manage energy isolation and lockout procedures for production equipment?
We design and verify energy control methods, including Lockout/Tagout (LOTO) systems, power isolation verification, and stored energy dissipation. Our solutions comply with UK regulations (PUWER) and EN ISO 14118 (safety of machinery).
What technologies do you use for dynamic safeguarding in robotic applications?
We implement advanced safety systems, including laser scanners, safety light curtains, and 3D area monitoring. These provide real-time protective distance control, speed reduction when humans approach, and full stop functions when necessary, meeting EN ISO 13855 and EN IEC 61496 standards.
How do you protect workers at access points to hazardous production areas?
Our access management solutions include interlocked guard doors with position monitoring, safety mat systems, and presence detection devices. These systems prevent access while machinery is in motion and verify all safety functions before allowing entry, complying with EN ISO 14119 and EN ISO 13857.
How often should safety systems be inspected?
We recommend formal inspections at least every 12 months, with weekly visual checks by your team, in line with PUWER requirements.
Can you upgrade our older machines to meet current standards?
Yes, we specialise in cost-effective retrofits, bringing legacy equipment up to current UK and EU compliance, including CE/UKCA marking where applicable.
What's the difference between SIL and PL ratings?
SIL (Safety Integrity Level, from IEC 61508) and PL (Performance Level, from EN ISO 13849-1) both measure the reliability of safety functions. We determine which standard applies to your equipment based on the relevant machinery safety requirements.
Do you provide safety documentation packages?
Yes, we supply complete technical files, including UKCA/CE declarations of conformity, risk assessments (EN ISO 12100), and test reports to ensure full compliance.