Robotic Integration Services
Custom Robotic Solutions for Manufacturing
Robotic Applications
We design robotic systems that enhance your workforce - from heavy-duty industrial robots for demanding tasks to flexible cobots that collaborate directly with your operators. Our solutions adapt to your production needs while maintaining strict safety standards.
Industrial Power Meets Collaborative Flexibility
Our expertise spans the full spectrum of robotic automation:
- Industrial robots for high-speed, heavy-payload applications requiring absolute precision
- Collaborative robots (cobots) for flexible, human-interactive tasks that need adaptability
- Hybrid workcells where both technologies combine their strengths seamlessly
Tailored Automation Solutions
For material handling, we implement vision-guided systems that maintain throughput while reducing product damage. Our palletising solutions combine robotic strength with smart pattern generation to handle mixed loads efficiently. Welding cells feature both industrial precision and collaborative safety zones for optimal results.
Safety-Integrated Design
Every solution includes risk-assessed safeguards, whether it's full safety-rated stops for industrial robots or force-limited operation for cobots working alongside your team.
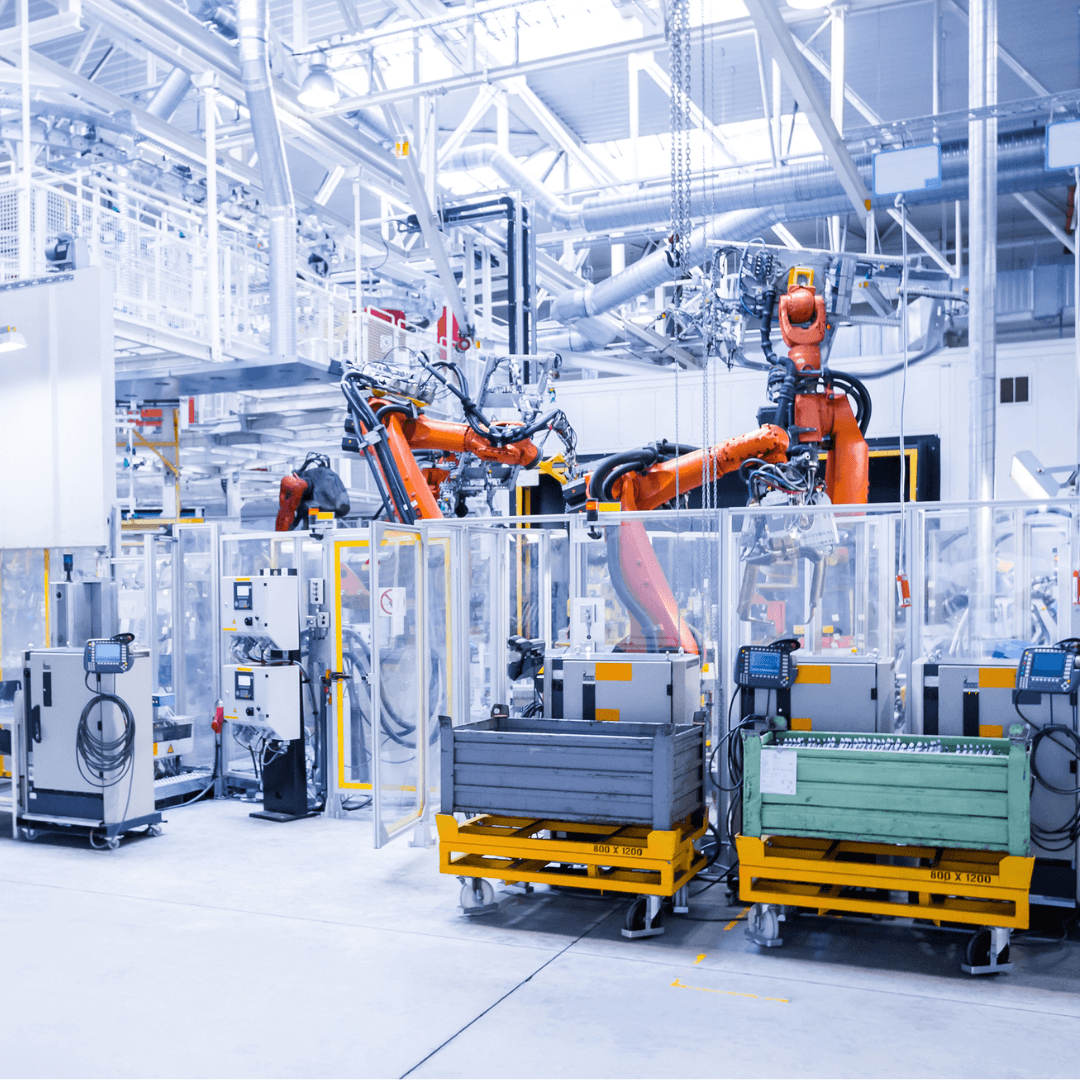
Our Robotic Integration Process
Application Analysis
Detailed workflow assessment and ROI evaluation
Concept Design
3D simulations and safety planning
Robot Selection
Optimal robot and tooling specification
Cell Integration
Full mechanical/electrical implementation
Validation
FAT/SAT testing with your team
Optimisation
Post deployment performance review
Ready to explore robotic automation for your facility?
Schedule AssessmentFrequently Asked Questions
Frequently Asked Questions
What's the typical payback period for robotic integration?
Most installations achieve ROI in 12-24 months through labour savings, quality improvements, and increased output.
Can your systems integrate with our existing PLCs?
Yes, we specialise in interfacing with PLC's including Siemens, Mitsubishi and other major brands.
How do you ensure safety in collaborative workspaces?
We implement risk assessments, programable safety controllers, and appropriate safeguards (light curtains, area scanners, or force-limited robots).
What maintenance do robotic systems require?
Typical maintenance includes annual mechanical inspection, periodic lubrication, and software updates - we can offer customised service plans.
Can you automate our legacy equipment?
Absolutely. We've successfully automated legacy machines with modern technologies and interface development.
Do you provide operator training?
Yes, comprehensive training covers operation, basic troubleshooting, and safety procedures tailored to your team's needs.
How does robotic welding compare to manual welding?
Robotic welding delivers 3-5x more consistent welds, 50% less rework, and can operate continuously without fatigue.